Intumescent coating types
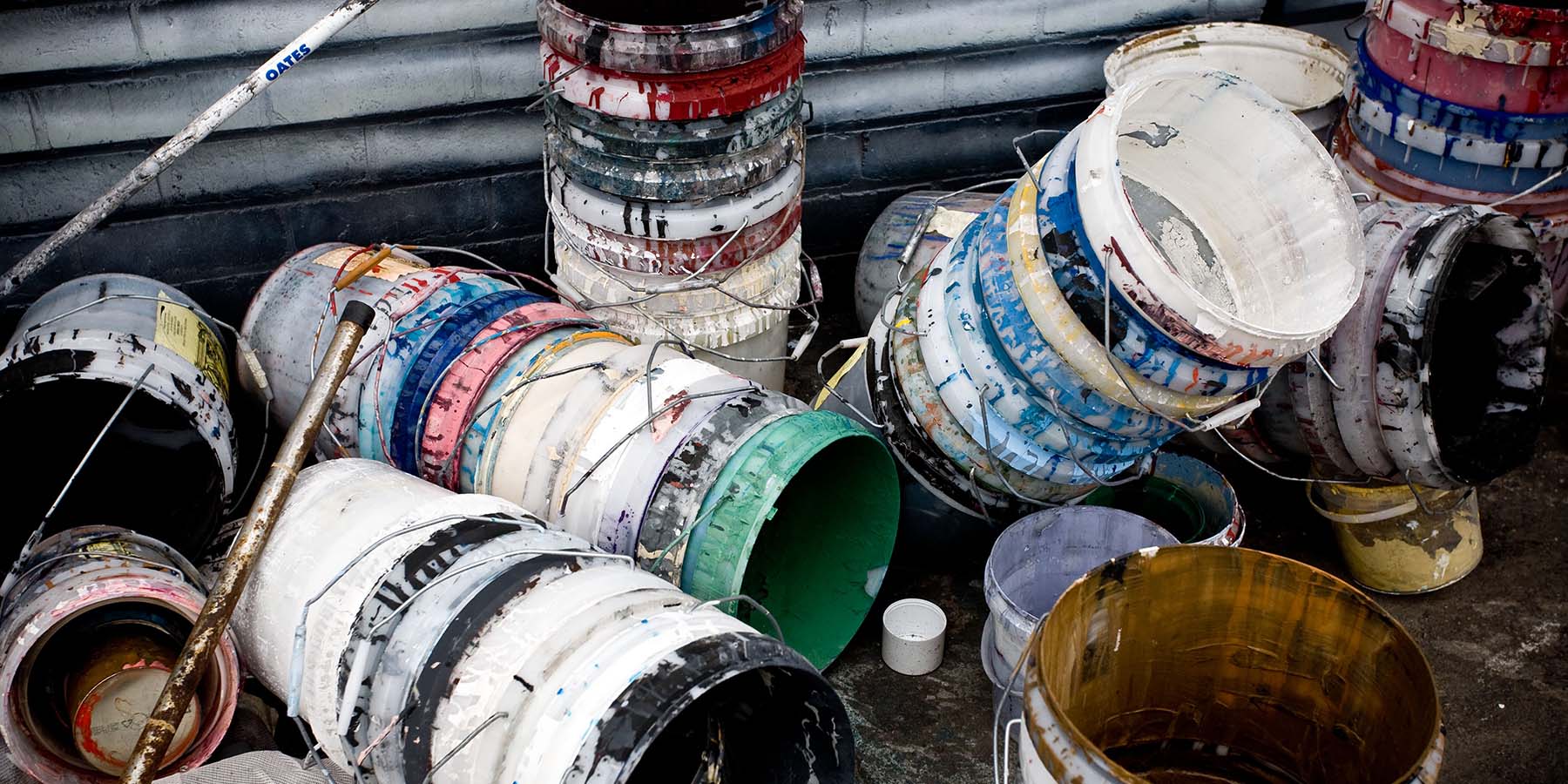
Intumescent is the newest fire protection methodology to come onto the market. Unlike boards and vermiculite, intumescent is a reactive material which expands to insulate structural steel in a fire event. Every intumescent has different material properties and therefore have different required thicknesses and expansion behaviour.
In 2013, the first ‘hybrid’ intumescent coating, Nullifire SC900 series, SC901 and SC902 was released. This technology combined the advantages of ‘thin film’ intumescent in respect to coating thickness and also introduced unique product performance characteristics that stood it apart from all other conventional intumescent coatings.
Solvent-based systems
Solvent-based coatings usually used in semi-exposed environments and are tested against weather and temperature variations. Solvent-based coatings tend to be more resistant to weather conditions as well as temperature changes and humidity. They also dry faster and have a smoother finish.
Advantages
- Suitable for internal steel or semi-exposed and exposed steel work when top sealed
- Can be applied off-site or on-site
- Relatively hard film when fully cured
Disadvantages
- If applied on-site it can be damaged by water if not fully cured
- Has high VOCs which can be an OH&S issue if applied on-site
- Requires multiple applications to achieve higher film builds
- Curing could take between 5 and 15 days depending on ambient conditions and film build
Example products
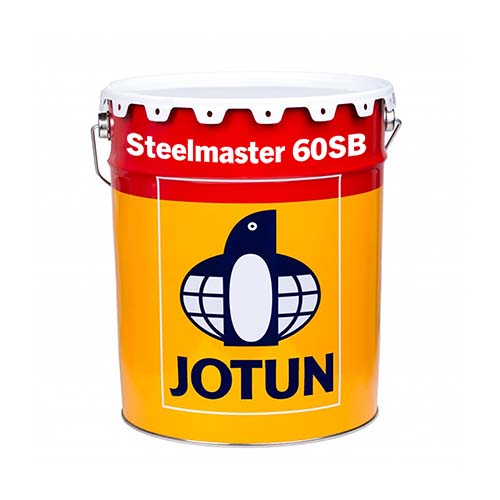
Water-based systems
Water-based intumescent coatings are a generally more eco-friendly and less "chemically-smelling" option. They are the least expensive and produce less odour, however these coatings are less tolerant to humidity and low temperatures and therefore may take longer to completely cure in such environments.
Advantages
- Very Low VOC
- Low odour so does not impact on other trades when applied on-site
- Can be applied to a smooth finish
- Relatively simple to repair
Disadvantages
- Can only be applied on-site in fully protected areas
- Very sensitive to high humidity or moisture
- Requires multiple applications to achieve higher film builds
- Curing could take between 5 and 15 days depending on ambient conditions and film build
- Can be prone to damage easily
Example products
Epoxy-based systems
Epoxy-based intumescent is typically used in harsher environments such as the offshore marine industries or the chemical industry because these coatings provide excellent hydrocarbon fire protection. Epoxy-based intumescent comes in two-parts which when combined, forms a very thick and durable film that insulates the steel member and is highly resistant to corrosion.
Advantages
- Low VOC
- Cures to a very hard durable finish
- Suitable for application for both internal and external steel work
- Generally applied off-site
- Relatively resistant to damage when handled or transported
Disadvantages
- Not generally suited to on-site application due to more complex application equipment requirement
- More expensive product in comparison to conventional intumescent coatings
- Higher film builds require multiple applications over several days
- Cured epoxy intumescent although hard can be brittle and be susceptible to impact damage
- Cured epoxy intumescent can crack and delaminate if coated steel deflects
Example products
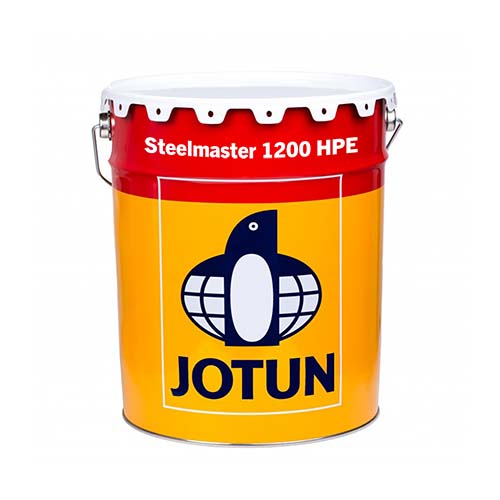